Services
LEAN PRINCIPLES. PRACTICES. PEOPLE & PROCESS.
Global BPO consultants
Serving the United States and Latin America
Will Duncan & Associates bring a unique blend of experience and perspective to the manufacturers, retailers and brands in the apparel, footwear, furniture and other sewn product industries. Will and his team of Business Process Optimization Consultants have worked with hundreds of international companies for many years and have gained a reputation of service excellence and trusted advisors.
Our focus is on eliminating time and waste in the entire manufacturing and product development processes and gaining efficiencies while instilling best practices at every step of our work together. We assist our clients to create more value for your business in margin improvements and revenues as well as to your own customers by maximizing the effectiveness of people and processes, providing insights and innovative approaches to issues from the boardroom to the factory floor.
In every project – small or large – we provide knowledge transfer and tips for operational improvement throughout our engagement as well as expert training and mentoring to optimize your workforce from the operators to supervisors, managers and engineers. Our holistic approach assesses every operational area and the tools and solutions they use thus, eliminating non-value added activities, redundancies of effort and other forms of waste resulting in significant reductions in time.
Brands & Retailers
Achieve Lean Product Development
Our goal for Brands & Retailers is to assist in identifying areas along the product development process that we can optimize through business process improvements, workforce efficiencies, cost savings and assisting your suppliers with the same for a truly collaborative and streamlined approach to lean product development.
Business Impacts: cost savings, speed-to-market, process optimization, higher margins, operations improvements
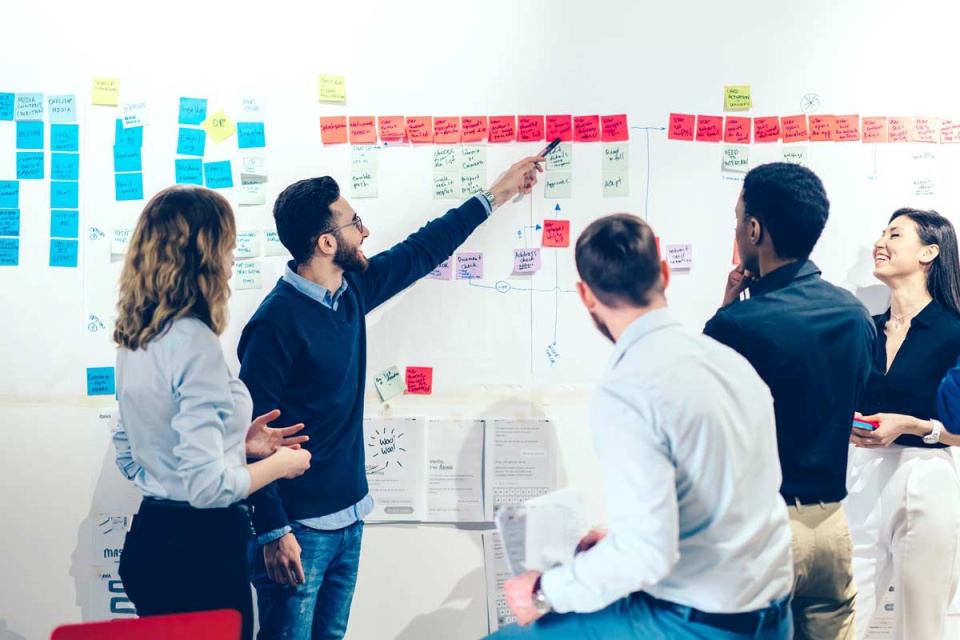
Business Process Optimization (BPO)
Optimize Process & People Productivity
Optimization of the Product Development Process and Lean Product Development is a goal for many of our clients. No matter what your goal, our BPO evaluates every step of your product development process from concept to design to production for new products, capturing use of technology, workforce challenges, opportunities for improvement with a focus on how to optimize the full business process and increase productivity across the operators. Typically, we on site for one to three weeks working side by side with management and team members sharing knowledge and tips where applicable. Your deliverable – a detailed recommendation for improvement step by step that you can execute internally or partner with our Business Process Optimization Consultants as a next phase.
Business Impacts: speed-to-market, process optimization, productivity increases, best practice knowledge transfer
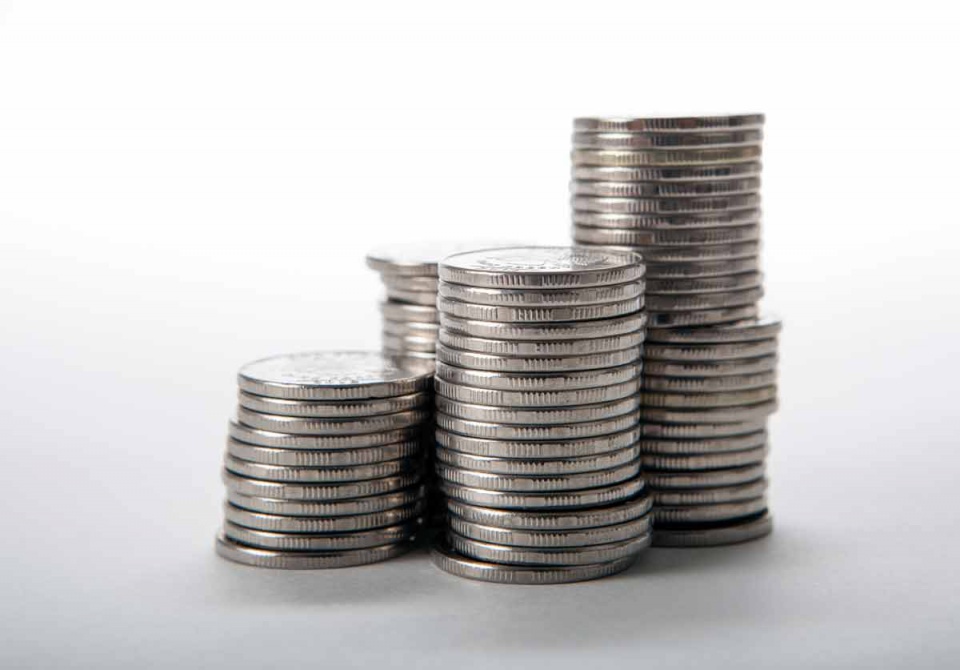
Product Costing Evaluation
Reduce Acquisition Costs & Improve Profits
Understanding the costs for materials & consumption, direct and added-value labor costs, sewing time, and shipping options can lead to more profitable outcomes for your production costs. Our 30 plus years working in manufacturing equips us with the knowledge and ability to audit actual costs and provide analysis on where to brings costs in line to protect margins and improve profits. In our time on site meeting with the operational areas engaged in your product costing, we will conduct a two-hour lean workshop to educate on lean processes, share knowledge and tips, and provide training tailored for your business and product categories. The deliverable – a detailed report of all the areas within your costing process where you can optimize processes and people to achieve cost-savings and higher margins.
Business Impacts: cost controls, higher margins, improve profits
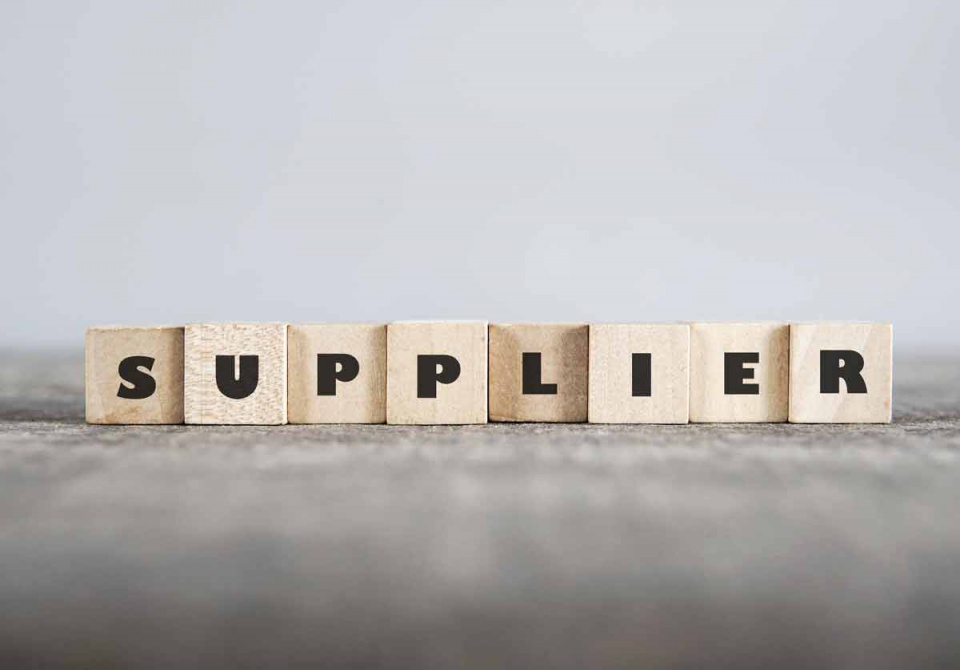
Supplier Assessments
Streamline Processes Across Contributors
The contributors to your product development cycles frequently include suppliers and partners as part of your overall enterprise. Why stop within the four walls of your business to optimize production and leave critical steps outside of an assessment and evaluation for improvement? Today, collaboration with suppliers is an ingredient to success, cost controls and management of your end to end processes from concept to design to production. We will leverage our extensive manufacturing knowledge working directly with your suppliers to identify areas to provide cost savings, margin increases and overall increased productivity for a win-win partnership. (link to manufacturing factory assessment to learn more)
Business Impacts: stronger collaboration, tighter cost control and cost savings, margin increase/protection
“WDA’s Business Process Optimization service was a valuable and helpful tool for our organization. Our specific project involved a broad subject with several cross-functional team members. This coaching enabled a collaborative and open forum that laid the groundwork for a much improved and better-defined process.
– Doug Tepper
Vice President Global Sourcing, Chico’s FAS Inc
Manufacturers
LEAN MANUFACTURING
Achieve Lean Manufacturing through Streamlined Processes, Standardized & Smarter Operations
Lean manufacturing involves continuous evaluation and review of every process step to eliminate or reduce waste or activities that do not add value to the customer while improving productivity and quality of goods manufactured. WDA have perfected our methodology to implement lean processes to help you achieve a lean manufacturing operation through our extensive years of BPO consulting and applying lean processes from design to product development to production focused on people, organization, processes and performance through step by step assessment and application of knowledge to improve operations.
We will perform an assessment or business process optimization depending on your current state of operations. We recommend best practices to optimize your operations through identified improvements, knowledge transfer and training for every level of your workforce. Our detailed recommendation of every operational area will provide a roadmap for execution by your team or the opportunity to partner with our BPO consultants to implement in collaboration with your company.
More than 100 global companies have embraced WDA’s Lean Manufacturing Methodology resulting in savings ranging from thousands to millions of dollars while gaining time savings and operational efficiencies ranging from 20% to 50% overall improvements.
Business Impacts: reduction in waste, higher workforce productivity, optimization of operations, increased performance
The WDA Lean Manufacturing Implementation Process
Designed to Coach Companies Through The Transition To Lean Teams
Manufacturing
Assessment
- Site Visit
- Document findings
Module
Design
- Establish sequence of operations & standard allowed minutes
- Determine Staffing& cross training Requirements
- Perform line optimization analysis
Equipment
Analysis
- Specify Machines, stands and attachments
- Prepare equipment list requirements and any identifed vendors
Training
& Mentoring
- 2 Day Management Workshop
- 2 Hour Employee Overview
- Team Selection & Cross Traning
- 2 Day Workshop Pilot Team
- One on One Coaching Supervisors & Workshop
Compensation
System
- Steering Committee workshop
- Data collection & Analysis
- Formalize Plan
Lean Line
Start Up
- Begin Production with Pilot Team
- Instill proper methods, efficiency levels and quality
Lean
Implementation
- Support at 2 weeks and 4 weeks
- Compliance to Work Methods
- Current Capacity and Efficiency of the Line
- Actual Production vs. Projections
- Engineering and Management Support
- Current Performance Against Quality Standards
- Equipment Performance and Technical Support
Assessments
Gain Quick Visibility into Areas for Improvement
Our Assessments identify opportunities for standards development, time savings, productivity gains and efficiencies across the operations. If an organization is not ready for a full Business Process Optimization study, our team will do an assessment over a few days onsite.
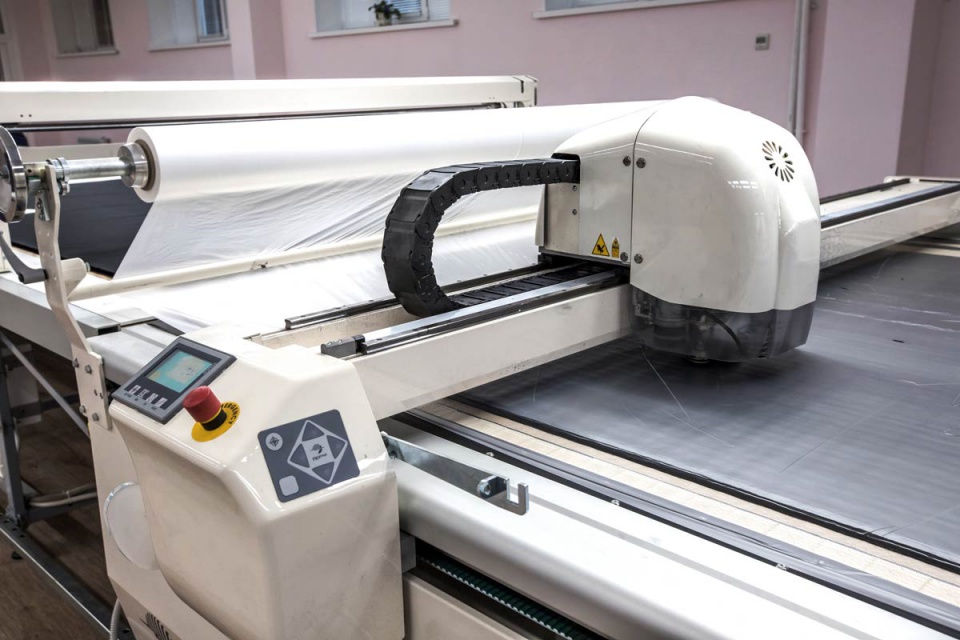
Factory Assessments
Shopfloor Optimization & Lean Manufacturing Readiness
A two to three-day onsite visit is all we need to review the various operational areas within the factory reviewing current business and manufacturing processes, operator training and cross-training methodology, scheduling and process flows compared to industry standards.
Our goal is to provide productivity improvement, cycle time reduction, and flexibility in a written report that will provide lean manufacturing readiness. During our time onsite, we will assess operators, supervisors and management providing knowledge transfer and tips where applicable to add instant value to your shopfloor. Our deliverable can be executed internally or with our expert consultants to create a lean manufacturing model factory.
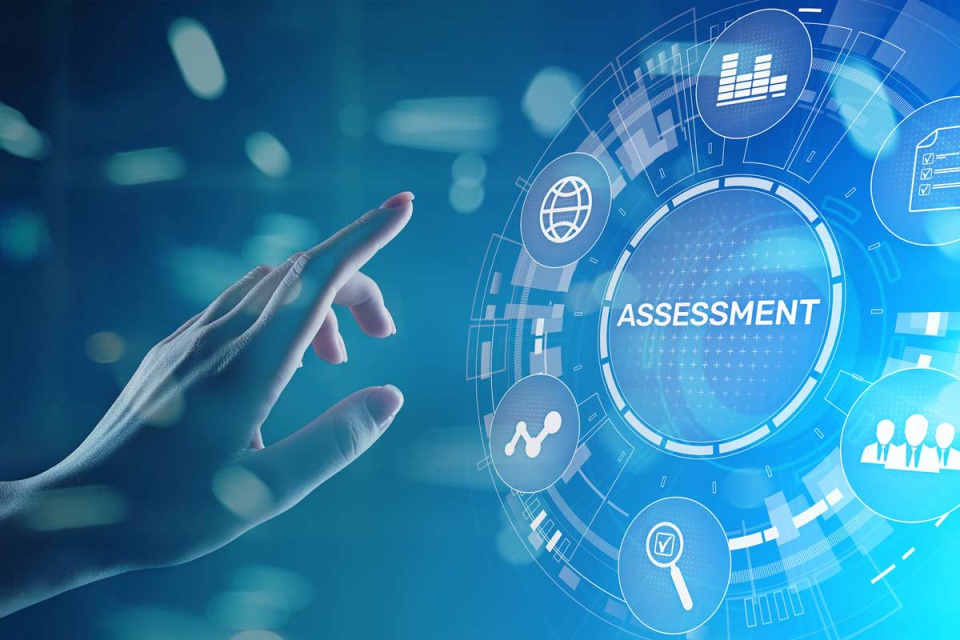
Technology Assessments
Best technology to Support business objectives
As part of the overall assessment or on its own, WDA will spend one day to assess your cross-functional operations and use of current technology to determine if an upgrade or a new solution is required to meet your specific requirements and objectives. We facilitate the identification of best fit solutions for your business as well as the impact to your workforce and provide training where required to achieve time saving and increased productivity.
Business Process Optimization Services (BPO)
Achieve Lean Manufacturing Process Improvements
Optimization of the manufacturing process with application of lean manufacturing processes is a goal for many of our clients. No matter what your goal, our BPO takes a holistic view to evaluate every step of your manufacturing process, capturing use of technology, workforce challenges, opportunities for improvement with a focus on how to optimize the full business process and people efficiencies to increase productivity from the factory floor to your boardroom. Your deliverable – a detailed recommendation for improvement step by step that you can execute internally or partner with us as a next phase.
Business Impacts: process optimization, productivity increases, best practice knowledge transfer
Workforce Training & Development
Build Great Organizations
We believe that effective training and development involves the transference of knowledge and teaching people applicable skills that help them to improve their performance, work environment and themselves. Most of the courses we teach are founded in fundamentals that are time honored and proven traditions in the industry. However, we actively seek and embrace available and upcoming disciplines and technologies that have the potential to affect the industry and our clients. We believe in a methodology that incorporates 80% hands on coaching and 20% classroom training to help ensure that concepts are understood and can be put into practice immediately.
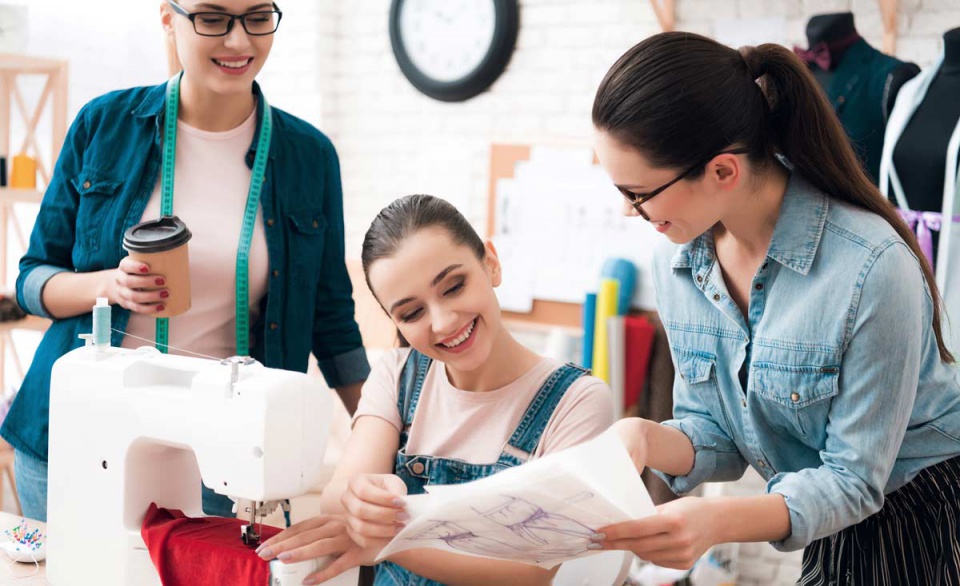
OPERATOR TRAINING
Gain efficiencies minimize injuries and turnover and increase product quality. Our train-the-trainer approach transfers knowledge to ensure long term success and our training approach is personalized based on your organizational needs determined during our assessment. We will provide hiring procedures and job descriptions with detailed curriculums for basic operator training and specific training programs.
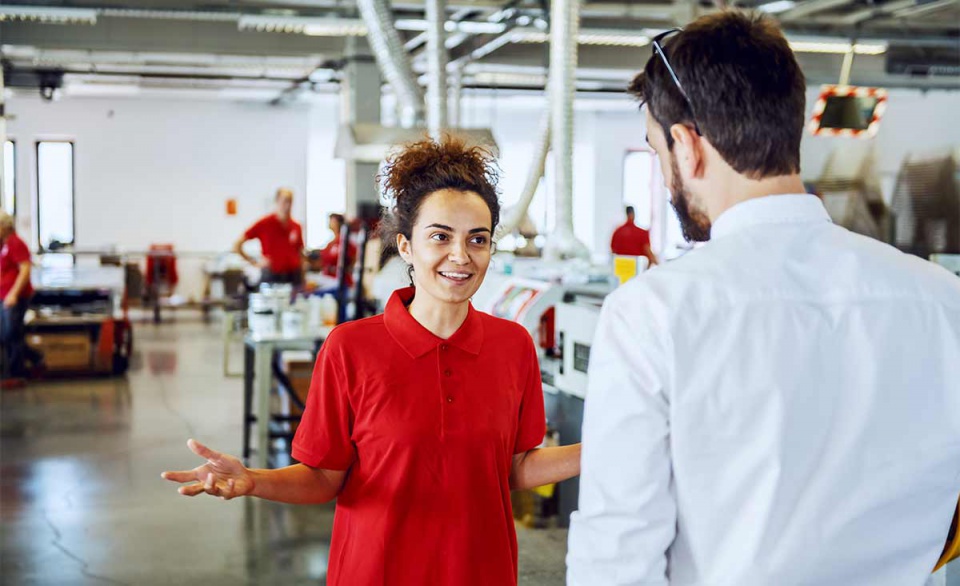
SUPERVISOR DEVELOPMENT
Many factors can affect your factory’s performance; however, none have a greater impact than the effectiveness of front-line supervision. Your factory will not achieve its potential with poorly selected and trained front-line supervisors. It takes years to develop effective front-line supervision. For this reason, it is important that a well thought out “formal” development program is in place to give the candidates every opportunity to succeed. Our comprehensive 14-week Supervisor Development Program starts with orientation, proper machine use and basic maintenance, hands on mentoring for continued knowledge transfer and supplemental monthly training to ensure success and a highly performing factory.
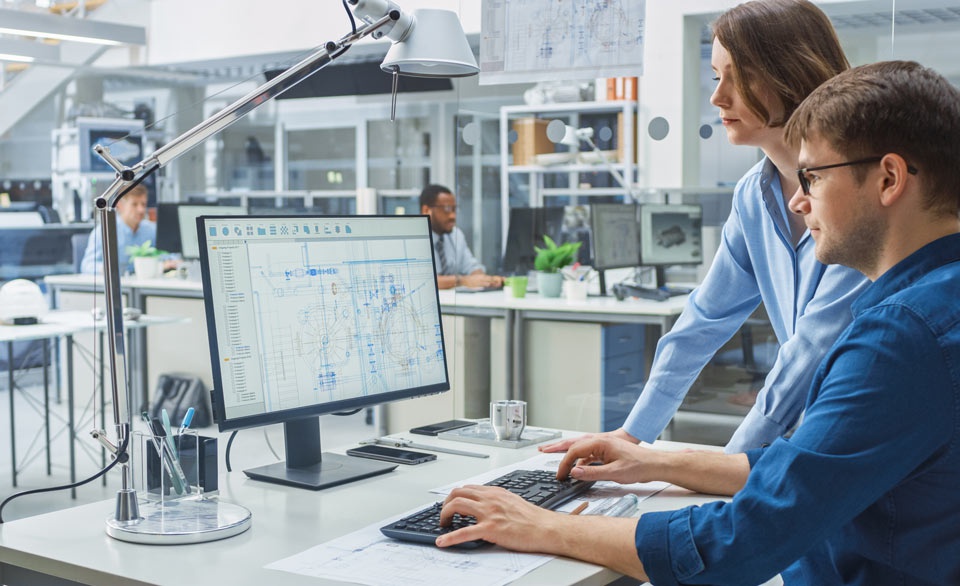
ENGINEER DEVELOPMENT
To compete as a sewn products manufacturer in today’s global marketplace requires that your factory is highly flexible, efficient and well-engineered. The role of the apparel engineer has never been more important. Many factories today have lost sight of the need for formal engineering practices such as efficient, consistent and well documented operational methods and workplace design, efficient plant layout and workflow, accurate product costing and standards development, and the application of lean practices. Whether experienced or a new hire, our Engineering Training and Development Program will help you meet and exceed the needs of today’s brands and retailers.
Engineering Services & Audits
Develop & Manufacture Quality Products
Our roots are in manufacturing. Over the past three decades we have partnered with our clients to facilitate improvements and changes in the way sewn products are made and how product information surrounding them is communicated. We work with factories all over the world to positively impact their bottom line and improve their ability to develop and manufacture quality products. Our proven methodology and ability to gain insights based on depth of experience across our team allows us to assist in finding solutions to meet business objectives and optimize your organization through a holistic lens across operational areas, processes, technology and tools, and skill sets. We cover a number of areas for your organization including operators, supervisors, engineers and management up to the board room.
-
Staffing Requirements & Operator Cross-Training
-
Production Planning & Scheduling
-
Standards Development & Performance Metrics
-
Compensation & Employee Recognition Programs
-
Plant Layout & Work-in-Process Control
-
Material Utilization & Methods Improvement
Increase efficiency. Get results.
Start today!